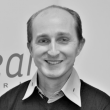
Business Development Engineer - Automotive, e-Xstream Engineering
After being graduated for his Master of Science on structural FEA in 1998, Sylvain Calmels worked for 5 years for Bertrand AG as structural engineer before joining PSA Peugeot Citroen group in 2006 as specialist in innovation and validation of new methodologies for FEA applied to NVH and non linear static behavior of BIW. Sylvain Calmels joined e-Xstream engineering in 2013 as Business Development Engineer for the Automotive Industry. Since then, his goal is to capture the industry needs in the field of material modelling from virtual testing to applications on full car and help in guiding the development of Digimat platform and related methods to fulfill the industry requirements.
Speeches
The increasing demand for vehicles weight reduction is driving Automotive OEMs to expand the use of short fiber reinforced plastic (SFRP) components to the under-hood applications. Benchmarking of production powertrains reveals that SFRP is commonly used for large components such as oil pans, valve covers, intake manifold and non-structural engine front covers. More recently, the use of the SFRP material was extended to the active side of the powertrain mount brackets. SFRP material includes a resin and filler; the resin is typically thermoplastic and the filler is made from glass fiber, carbon fiber or sometimes natural fibers. The viscoelasticity behavior of the SFRP material is dominated by the resin while its stiffness is dominated by the filler. The SFRP materials are injection molded with fibers that have aspect ratios ranging from10 to 25 (ratio of fiber length/ fiber diameter). In contrast with metallic components, implementation of SFRP components is very challenging due to the high temperature environment and the reduced stiffness inherent to this type of material. These challenges increase the risks for objectionable noise and vibrations associated with these components. The components macro-behavior is driven by its micro-structure resulting from the injection molding process that creates a heterogeneous distribution of the fiber orientation. Consequently, the local component behavior will be driven by the anisotropic nature of the SFRP material. For this reason, the simulation of the NVH performance of such components requires a material model that captures this local behavior. The design of these components should not be limited to the optimization of the geometry but extended it to include the choice of the material (resin and filler) and the optimization of the fiber orientation. This paper presents an integrated analytical process to optimize the material microstructure for improved NVH performance of SFRP components. The process combines: (a) Anisotropic material modeling, (b) Mold flow analysis, (c) Finite element analysis and (d) Multi-disciplinary optimization. Results obtained in the case of an engine mount bracket will be discussed in this paper. In this case, the impact of the material microstructure on the dynamic compliance of the bracket will be studied.