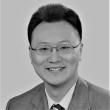
Professor and Site Director, NSF Center for e-Design, Wayne State University
Kyoung-Yun Kim is a professor in the Department of Industrial and Systems Engineering at Wayne State University, where he directs the Computational Intelligence and Design Informatics (CInDI) Laboratory. Dr. Kim’s research focuses on Design Science; Design Informatics; Manufacturing Awareness on Design; Semantic Assembly Design; and Product Life-cycle Modeling. Dr. Kim has received over $10M by external funding from several U.S. federal agencies including NSF, DMDII, NIDRR, VA-CASE, DOD, and DOE, the Korean Ministry of Knowledge Economy, and industries including Ford, GM, and GDLS. He has published over 100 top journal papers conference papers in proceedings, and numerous technical reports and presentations. Currently, Dr. Kim is a Site Director for the NSF Industry and University Cooperative Research Center (I/UCRC) for e-Design. Dr. Kim is a member of a steering committee to integrate the GM PACE infrastructure into Wayne State’s engineering curriculum and Electric Drive Vehicle Engineering program with the funding from DOE. Dr. Kim is a Fellow of the Society of Design and Process Science. He currently serves a Co-Editor-in-Chief of Journal of Integrated Design and Process Science. Dr. Kim received top cited article award (2005-2010) from Journal CAD and 2003 IIE Transactions Best Paper Award. Dr. Kim was an invited professor at Université de Technologie de Belfort-Montbéliard (UTBM), France, 2017 and was a visiting professor at Kyung Hee University, South Korea, 2014. Dr. Kim’s education includes a Ph.D. in Industrial Engineering from University of Pittsburgh, and a B.S. and M.S. in Industrial Engineering from Chonbuk National University, South Korea. Dr. Kim is a member of IIE, SDPS, ASME, and ASEE.
Speeches
This talk is to introduce Wayne State University’s College of Engineering Digital/SMART Manufacturing Demonstration Center (WSU D/SDC) that offers a state-of-the art, industry partnered manufacturing environment for innovative research projects and to educate the next generation workforces in the coming evolution of manufacturing. Students and researchers alike have the opportunity to interact with real- time manufacturing, inspection, design/engineering data integration via Cisco Systems platforms and fully sensored advanced manufacturing processes. The D/SDC houses a variety of advanced manufacturing equipment/software, connected together with secured systems infrastructure with Cisco. This enables research and education not only on advanced equipment, such as collaborative robots, additive manufacturing, computed tomography (CT) scanning, and automated laser scanning, but also on the data management, storage, infrastructure, and security critical for IoT, Industry 4.0, and SMART Manufacturing. Aforementioned equipment and design software including CAD/CAM, and design optimization (including modeFRONTIER) have plug and play capability into the Cisco System digital thread. With D/SDC facilities, the Wayne State team is realizing a connected Resistance Spot Welding (RSW) weldability certification concept. RSW is one of the critical and common joining methods in sheet metal-based industries (e.g., automobile, electronics, and aircraft manufacturing). Certification of RSW weldability is crucial to validate the quality and safety of final products. However, the current RSW certification process has multiple challenges. The first challenge is that it is difficult to predict the weldability of new (or combination of) materials that are constantly required in order to satisfy new product functionalities. The second challenge is that a significant number of physical tests are required to certify a welding process for the new combination of materials. In the auto industry as an example, one weld design can require 300-600 tests to certify weldability. Thus, feasibility decisions can be delayed by 8-10 weeks. With the aid of modeFRONTIER, a connected platform is under development to integrate RSW data driven prediction systems, physical models, in-situ RSW sensors, and RSW weld quality metrics for real-time learning to make decisions per individual RSW sample. In this talk, use cases showing the multiple criteria optimization to estimate the welding control parameters are presented in the context of the connected weldability certification concept.