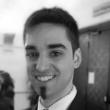
Mechanical Engineer, University of Trieste
Giulio Scrimali graduated in Mechanical Engineering at the University of Trieste (Italy). In 2016 he participated in an Internship with Elettra Sincrotrone Trieste. He spent his master thesis internship at the European research center European XFEL GmbH, in Hamburg, Germany, where he collaborated with the Sample Environment and XRAY Optics and Transport groups. At the beginning of his career as an engineer, he has interest in computational fluid dynamics simulations and a strong passion towards research.
Speeches
The project originated from the collaboration between the University of Trieste and the European XFEL research centre. It was developed in conjunction with the studies in the design of a new microfluidic injector for gas flow focusing of liquids jets, employed for the delivery of experimental samples in vacuum test
chambers used for experiments with synchrotron light, in the specific case emitted by a Free Electron Laser (FEL). The device, named Gas Dynamic Virtual Nozzle, is mounted on the in-vacuum experimental chamber and uses a coaxial gas stream to focus a liquid flow exiting from a micrometric capillary. Both the gas and the liquid are conveyed through a micrometric sized aperture: the dynamic forces of the gas together with the liquid superficial tension create an elongated meniscus at the liquid channel outlet, at the point of which a liquid jet is emitted, with a diameter smaller than the liquid capillary diameter. The study focused on the numerical fluid dynamics modeling of the device. With some geometrical and theoretical simplifications, the solution of the problem was performed with a two-dimensional, axisymmetric, steady-state model. The fluid dynamics calculations were performed with the proprietary CFD suite of ANSYS INC; the effective calculations were done with a specialized bi-dimensional solver of the FLUENT software. It was shown that the steady state model is able to describe the liquid focussing phenomenon. Once the model was proved working correctly, it was used in an optimization process to find the optimal liquid and gas inlet parameters to inject efficiently samples in the case of experiments with FEL light. The optimization process was performed with the specialized software modeFRONTIER, by ESTECO. Experimental measurements were carried out to obtain real data to compare with the numerical simulations results. Further analysis revealed a difference in the expected pressure level in the experimental measurement, induced by the difference in the geometry. Finally, a tridimensional analysis was performed to validate the generality of the results. Some advice to better the device design were derived from the results found, to be used in the next iteration of the designing process. modeFRONTIER capabilities were used through the whole project, from data analysis to job distribution using the GRID Manager, and helped to secure results in short times.